INSIDE LOOK
FEV’S VARIABLE COMPRESSION CONNECTING ROD
It has been years—over a decade, in fact— since reducing emissions or improving fuel economy was either easy or cheap. In the early days of engine efficiency upgrades, you could get a 1-percent improvement at low cost. An early example: Simply changing piston ring design for less blow-by dramatically improved hydrocarbon emissions.
Today, we’re at a point in engine technology and advancements where every single percentage is hard won and costly. Yet, there are still solutions that result in over 5-percent improvement in CO2 on the New European Driving Cycle, like this connecting rod that delivers variable compression ratio.
FEV is an engineering consultant company based in Aachen, Germany, with an office in Auburn Hills, Michigan. We’ve been following development of this connecting rod for five years, but the idea of variable compression ratio goes back more than a decade.
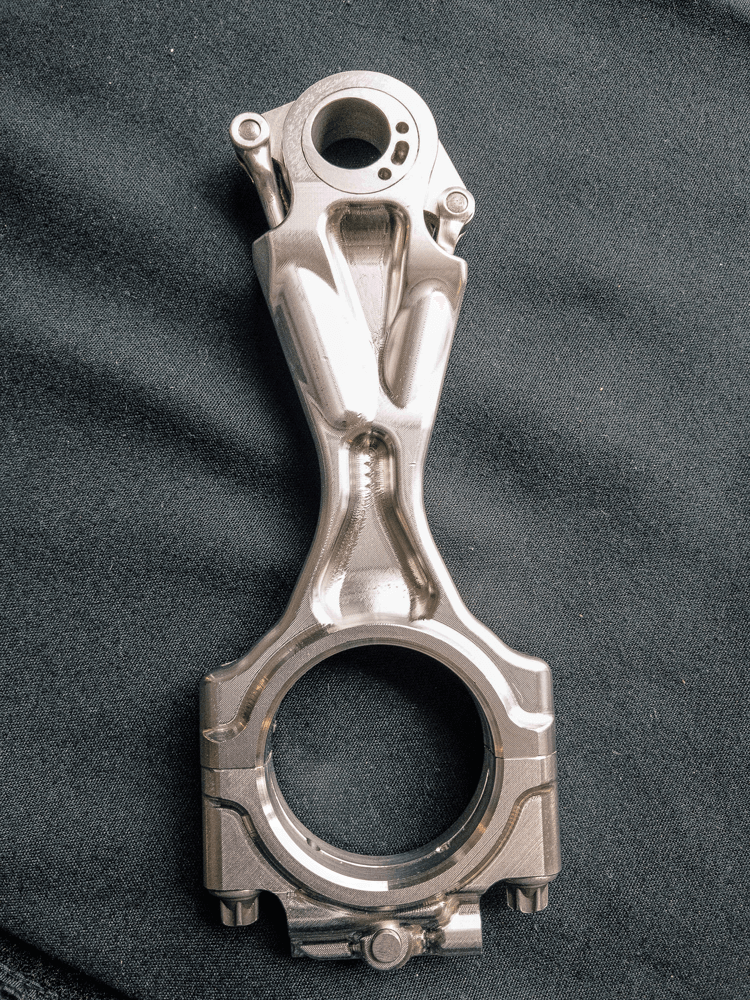
There was an attempt to continuously vary compression ratio by moving the entire crankshaft up and down. Moving the crank vertically meant the transmission had to move along with it, or involve some energy transfer mechanism. The last straw in that development was that there was no way to easily adapt a fixed center line change with an existing transmission (think about it). A later solution moved the head itself, but both had significant challenges. Why continuously variable compression? At the time, engineers thought it necessary to linearly move the compression ratio across the entire engine map.
The next evolution was to look at the connecting rod. Earlier designs were based on an eccentric bearing at the crankshaft. Now, FEV’s con-rod design uses an eccentric bearing at the wrist pin to move the piston up and down from its peak in the cylinder bore. If you are using an eccentric bearing you deliver what becomes a two-step scenario.
While you could force continuously variable compression, this requires energy input. If you require energy input to actuate the thing, whatever the solution is, it’s not going to work out. The whole objective is to get better fuel economy, not create parasitic losses and reduce the overall benefits you could achieve.
So, back to two compression ratios. FEV’s R&D and engine testing facilities, and their customers and their engine development, have suggested that INSIDE LOOK FEV’S VARIABLE COMPRESSION CONNECTING ROD most of the benefit of in nitely variable compression ratio can be achieved with only two ratios. We spoke to Dean Tomazic, vice president of FEV, about this connecting rod. He says you can achieve most of the benefit, approximately 80-85 percent of the more complex fully variable system, with only two ratios.
Why so much for so little?
The primary benefit of compression ratio changes is a significant reduction in fuel use and every truck maker is scrambling to meet 2025 emissions and efficiency requirements. Because you can set the compression ratio across the engine map, taking full advantage of the part of the map you’re operating in, you can get torque improvements, especially at the low end.
The benefit of being able to change the compression ratio, depending on where you are in the map, opens the engine’s operating area significantly. You can take advantage of any fuel’s characteristics and adjust the compression ratio for the characteristics of the fuel you’re running.
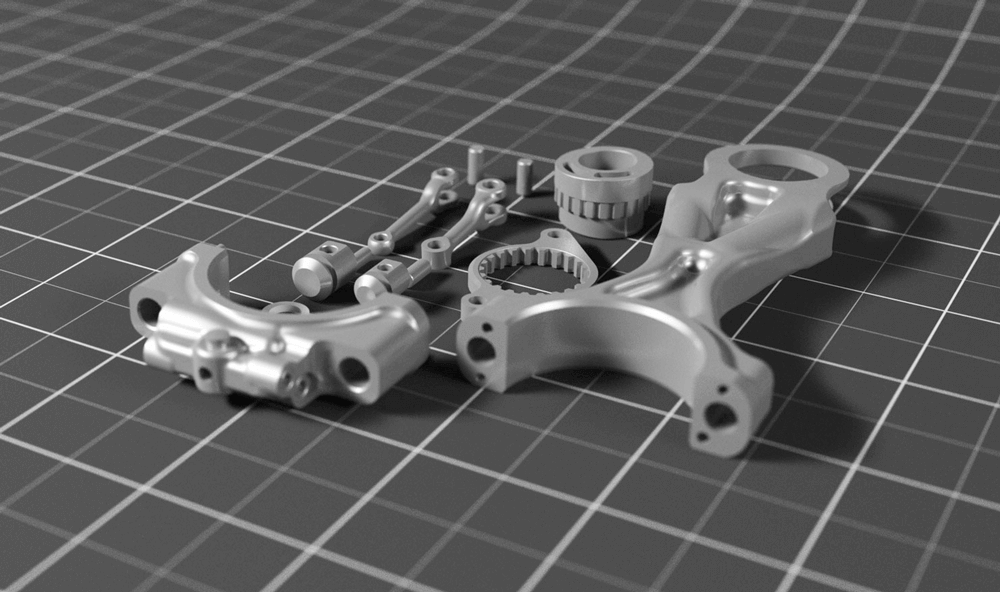
In a diesel engine, when operating under low load conditions you can use high compression ratio, which provides a dramatic increase in efficiency. Variable compression has another advantage for diesel engines: decreasing hydrocarbon emissions. As you move towards high load, you can set the compression ratio lower, which helps reduce particulate emissions without significantly increasing NOx output. If you were to leave compression ratio stable, to get higher ef ciency you’d have to increase the process temperature. As we all know, when you increase temperature, NOx goes up. By being able to play with compression ratio you now have the ability to nearly at-line your NOx emissions and still reduce particulates. With variable compression, you can increase your full load power and have the ability to get better efficiency without changing peak ring pressure in the engine.

The Parts and Pieces
Diving into the details, this solution has its mechanism driven by gas forces in the cylinder and reciprocating mass forces. There are oil galleries in the connecting rod, but the oil pressure is only used to lock the con-rod into one setting or the other. Actual eccentric movement is done by combustion pressure or kinematics—the piston moving up or down. The advantage to this is, we’re not throwing away energy to move the piston up or down, all we’re doing is using the oil pressure coming out of the journal side as a way to hold the connecting rod in position. Activation time is 0.2-0.7 seconds.
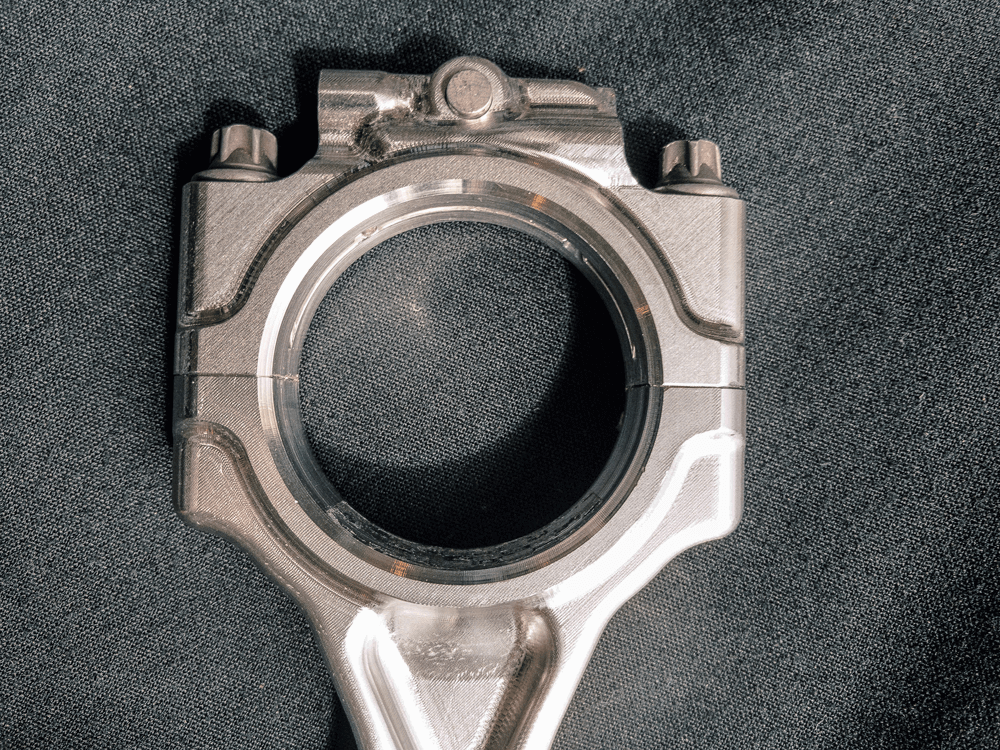
While the rod appears normal at rst glance, inside are two support rods with small pistons and oil galleries. At the bottom, a small shift valve directs oil in the proper direction and holds in that position.
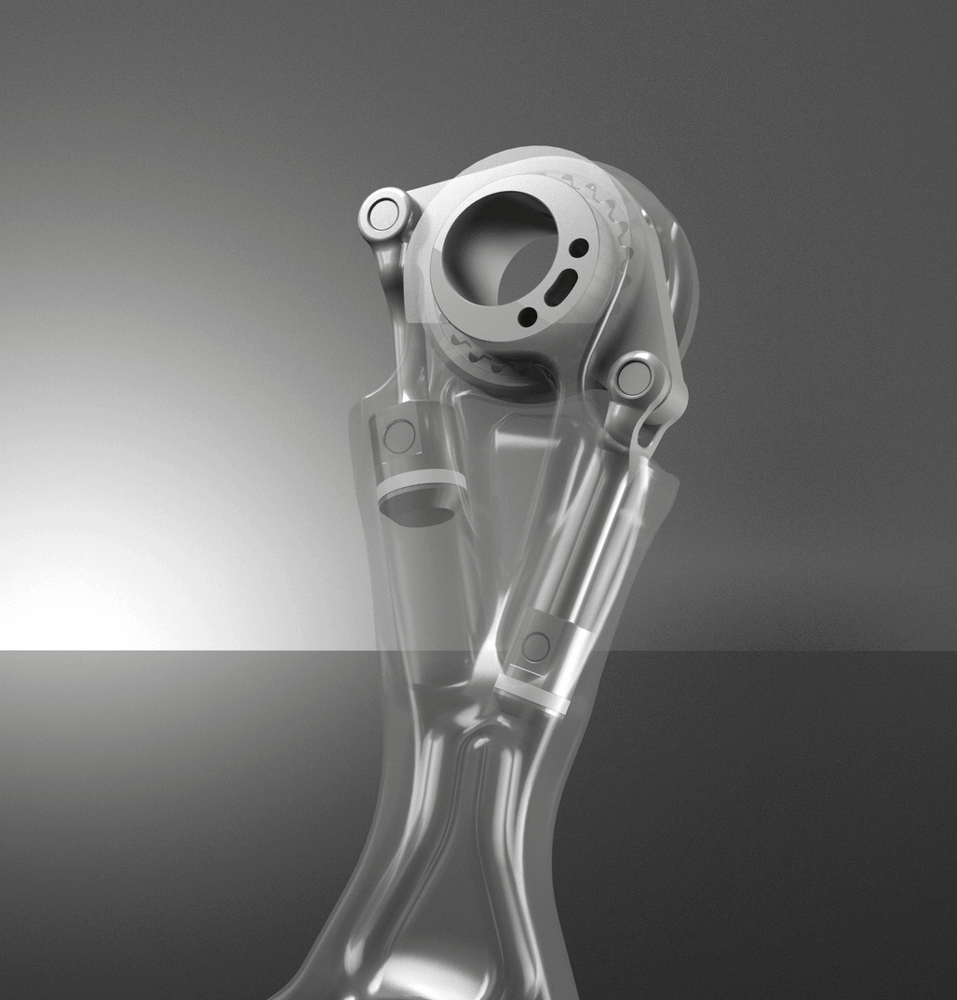
We asked the affable Mr. Tomazic about the cost of complex parts and if there are concerns with making them. He tells us: “We’ve collected a lot of experience and know the dos and don’ts about fabrication and materials. We would suggest to any manufacturer or supplier that we be heavily involved in production and machining. We didn’t make a lot of them, but understand the tolerance, machining, assembly, and materials. We want to use our experience to ensure success.”
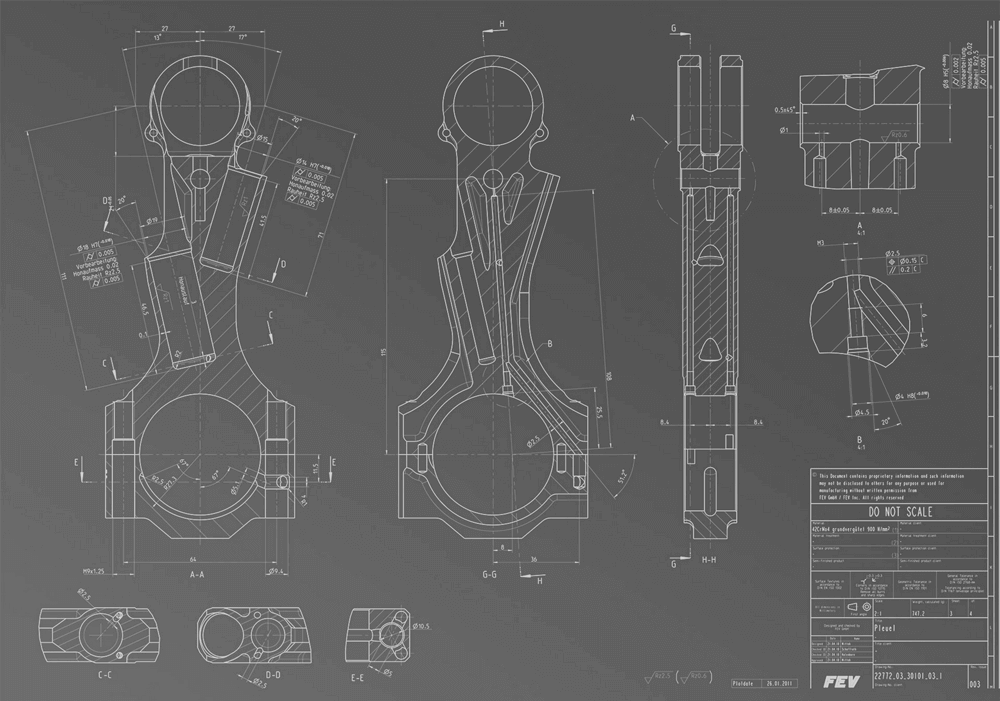
We concluded our chat by asking the inevitable: How soon and how much? Tomazic responds: “Several manufactures are looking at taking this into production and the time from contract to implementation depends on the supplier. Is that rod supplier already working with FEV and knows what’s being done or starting at zero? So, if you look at validation testing on the road it would take a few years depending on how quickly a supplier can ramp up production.
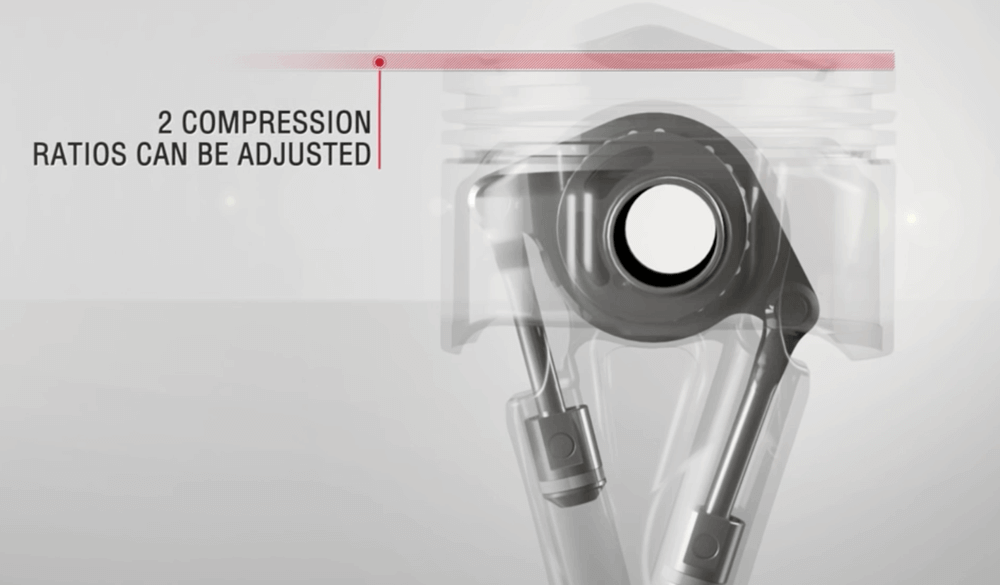
“With a potential improvement of 4-7 percent on the New European Driving Cycle, this is quite remarkable. All the low hanging fruit, $20 for 1 percent has been picked. Every manufacturer is now looking at more expensive solutions and variable compression ratio represents a big hammer in CO2 reduction and better fuel economy.” Oh, and it’s not pie-in-the-sky. There are validation vehicles out testing today. Does this ensure we’ll see this system? No, but the chances are good.